CAMPOFRÍO once again trusts ULMA Drainage for its factory in Burgos
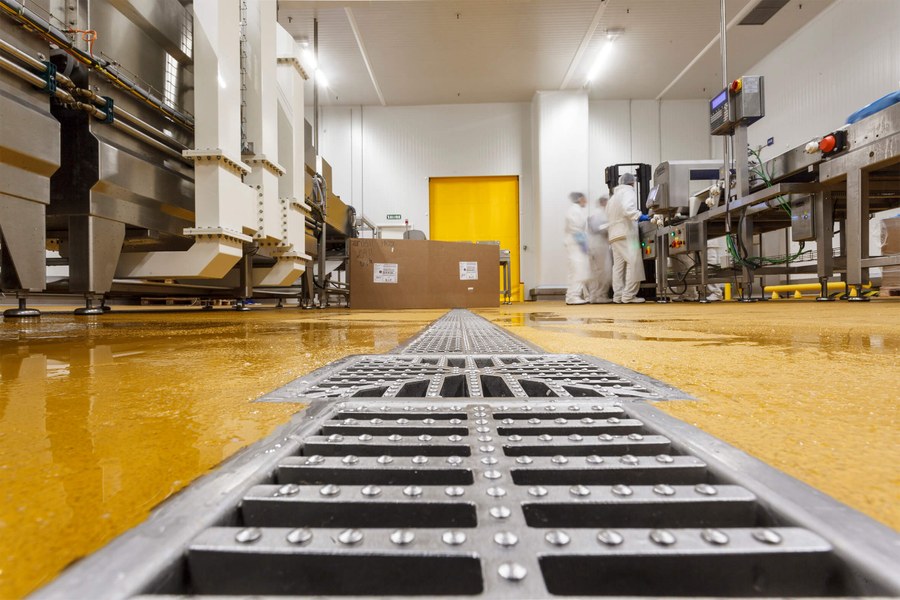
Thanks to an investment of €225 million, an area of 99,000 m2 and a production capacity of more than 100,000 tonnes per year, the new CAMPOFRÍO plant in Burgos – which began operating two years after a fire destroyed the old plant – is the largest and most modern meatpacking complex in Europe.
ULMA Architectural Solutions participated in this project supplying the drainage system in stainless steel, which features products specially designed for the meatpacking industry in order to ensure the required hygiene.
In total, more than 1,000 lineal metres of stainless grooved channels and channels with the Hygienic Pro® grid and over 400 stainless drains of different types have been installed, in addition to watertight covers for inspection chambers. The ULMA stainless drainage system is specially designed to evacuate, in an efficient manner, organic waste that accumulate in the industrial meat processes, allowing a fast cleaning and guaranteeing an excellent antibacterial behaviour. The Hygienic Pro® grille has an appropriate design to facilitate cleaning.
Campofrío already relied on the ULMA stainless drainage system for its pizza factory in Soria a few years ago. The experience was very satisfactory, to the point that the company showed great interest in including this product line in the project of the Burgos plant. It is a product of very high quality, which allows and favours cleaning, ensuring maximum hygiene and durability while complying with all requirements and regulations of the sector.
In addition to the stainless drainage system in its interior, 300 lineal metres of the KOMPAQDRAIN® drainage channel were supplied outside the plant. It is a novel compact channel made of polymer concrete, in which the channel and the grid form a single piece, ensuring greater resistance and rigidity. Thanks to its innovative MAX FLOW® system, which is based on the curved design of its water inlets, it is possible to accelerate the speed of the water inside its own channel in such a way that it causes a self-cleaning effect in a natural way and increases the capacity of sewer system.