ULMA, IK4-Tekniker and EHU-UPV declared No. 1 by European Robotics Challenges in the collaborative environment project
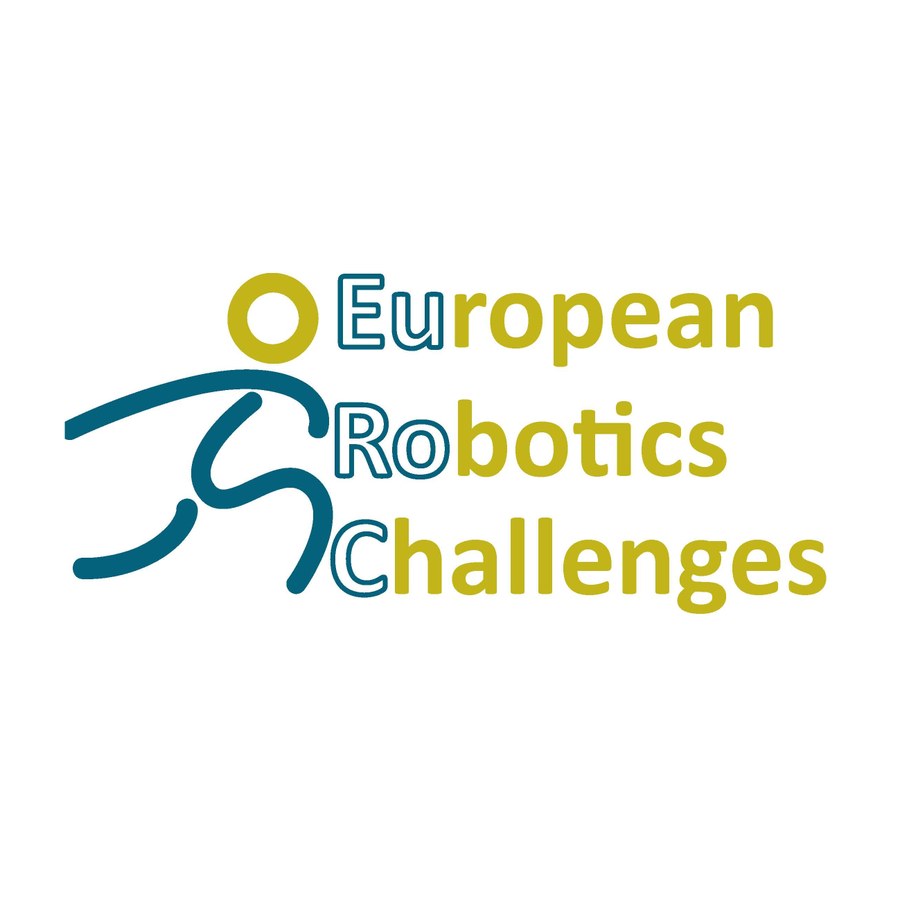
The project developed by ULMA Handling Systems, IK4-TEKNIKER and EHU-UPV University has been chosen from among 15 projects that were presented at the EUROC (European Robotics Challenges), and they were declared the winners of the best consortium category (RSAII) under the Project “FLECOOP: flexible unit picking system in collaborative environments for preparation of orders in distribution centres”.
Well-known names such as Airbus and Peugeot Citroën are some of the companies that took part. ULMA and IK4-Tekniker have been involved in this project since 2015 and the phases completed have been varied, physically developing the prototype proposed for the final phase: the Collaborative Robot.
The challenge consisted of obtaining an automatic unit picking prototype in human-machine collaborative environments for order preparation in distribution centres. The main approach was to provide a hybrid solution in which robots and humans shared the same work space, combining a high level of automation, monitoring the work area and guaranteeing workstation safety at all times. Detection of the objects handled by the robot takes place by 2D and 3D vision which allow automatic handling for pick & place operations.
Today, the robot makes it possible to assess the viability, acceptance and efficiency of this new work concept of robot-human collaborative environments without physical barriers. This will reduce the number of errors, the cost of the picking process, the space required in comparison with traditional solutions with robots, working conditions will be improved, etc.