GAZIMO monitoring sensors
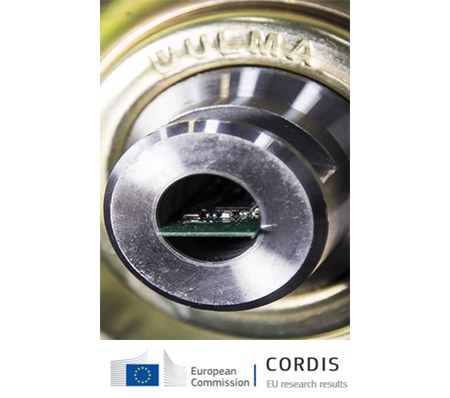
We attach the publication.
Roller sensors that prevent breakdowns and increase the efficiency of conveyor belts
Eventually, conveyor belt rollers tend to break down, which generally requires the belt to be stopped for repair or replacement. The GAZIMO surveillance sensors detect issues before they materialise, saving time and money whilst increasing security.
Conveyor belts are used to move materials in industries such as mining and metallurgy. The most vulnerable parts to breakdowns are the rollers. Virtually anything that can damage the belts, such as overloads or a dirty belt, can impact or harm the performance of the rollers. When this happens, the remaining rollers carry more load and may break as well. At some point, the conveyor will no longer be able to run, so it will need to stop while parts are being repaired or replaced, with accumulated maintenance costs and lost capacity. Unfortunately, current methods for identifying issues, usually based on manual inspections, are inaccurate and ineffective, as they detect problems only after they are made patent. The European-funded GAZIMO project works on the development of rollers with integrated sensors, a communication module and autonomous power generation. These rollers provide real-time technical data on their performance. By indicating their exact location, they allow repair or replacement before causing a breakdown of the conveyor. “At ULMA Conveyor Components, we have been designing and manufacturing rollers for more than sixty years and we know how to build durable rollers in very harsh environments. We are proud to have developed GAZIMO from scratch. At that time, there was nothing on the market for the monitoring of the rollers”, said Egoitz Jiménez, General Director of ULMA and project coordinator. Jiménez appreciated the EU funding that allowed the team to develop a business plan leading to the sale of the system.
Roller monitoring system
The GAZIMO sensors monitor each of the rollers from inside, delivering accurate information about their individual and collective condition. The communication modules on each roll create a wireless network of sensors that sends updates to the maintenance team.
The system alerts staff to potential issues through alarms, which can decide when to rectify the issue based on location and severity. ULMA engineers also analyse this information to improve the rollers and extend their service life. GAZIMO also has a new energy collection system that captures the energy generated by turning the rollers. “Because a lot of energy is required continuously, our engineers had to adjust the communication protocols so that they consumed less. The new generation will use batteries that can last as long as the average service life of a roller”, explained Jiménez. The team installed the prototypes of rollers with GAZIMO monitoring capacity in mines in Australia, Spain, Norway, and Peru. Testing in these highly varied electromagnetic environments has led to the introduction of changes to the GAZIMO communication system, but at the same time, they helped to validate the system as a whole.
Greater security with lower costs
The GAZIMO controlled rollers will help to increase safety in dangerous environments such as mines. Currently, to check for issues, workers walk on moving conveyors. The system will also reduce waste generation, as broken rollers can be replaced before causing further damage, increasing their efficiency and reducing the energy consumption required to operate the belt. “The GAZIMO design could save millions of euro for many industries and become integrated into automated mines, in places that are not accessible or safe for people”, added Jiménez. The team is currently working on the design of GAZIMO 2.0, which will feature an even stronger surveillance system and a more reliable communications module. After the prototyping phase, ULMA Conveyor Components proceed to market the system in mines with which a relationship has already been established.